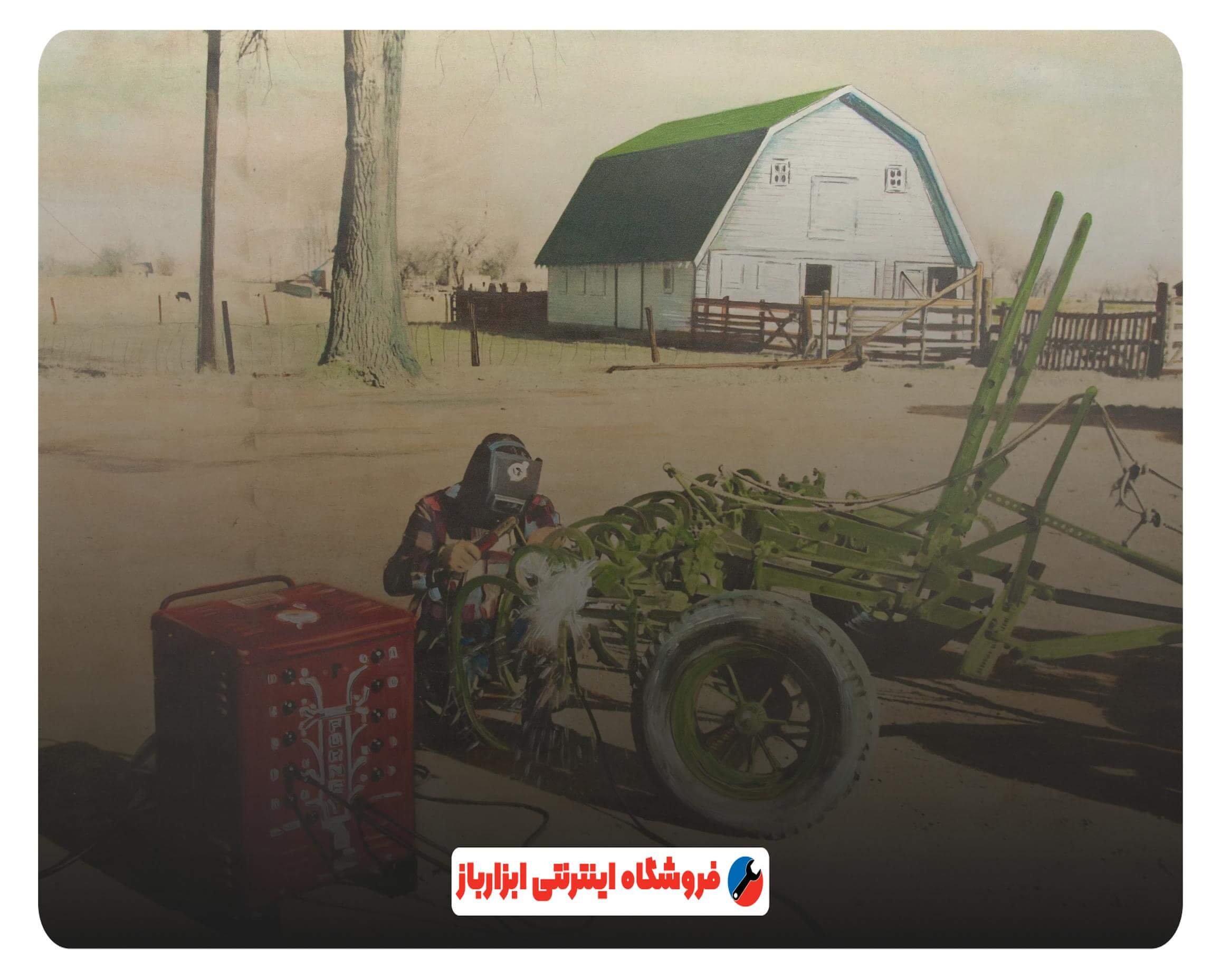
دستگاه جوش چیست؟
دستگاه جوش ابزاری است که برای ایجاد اتصالات دائمی میان مواد مختلف، به ویژه فلزات، استفاده میشود. این دستگاهها با استفاده از گرما، فشار یا ترکیبی از هر دو، مواد را به هم متصل میکنند. فرآیند جوشکاری معمولاً برای ساخت سازهها، تعمیرات صنعتی و حتی در پروژههای کوچک خانگی استفاده میشود.
تاریخچه دستگاه جوشکاری به اختصار از مراحل مهم توسعه تکنولوژی جوشکاری بیان میشود. جوشکاری یکی از قدیمیترین روشهای اتصال فلزات است که به قرنها قبل بازمیگردد. در اینجا، به طور مختصر به مراحل مختلف تکامل این ابزار مهم اشاره میکنیم:
جوشکاری ابتدایی
در دوران باستان، انسانها از روشهای ابتدایی برای اتصال فلزات استفاده میکردند. آهنگری و حرارتدهی دستی یکی از رایجترین تکنیکها بود که از طریق آن، فلزات به یکدیگر متصل میشدند.
انقلاب صنعتی و تحول در جوشکاری
در قرن ۱۹ میلادی و با شروع انقلاب صنعتی، نیاز به ابزارها و ماشینآلات دقیقتر، باعث شد تکنولوژیهای جدیدی برای جوشکاری توسعه یابد. در این دوران، جوشکاری فورج (forge welding) با استفاده از حرارت و فشار بهبود یافت.
معرفی دستگاه جوش الکتریکی
در دهه ۱۸۸۰، فرآیندهای جوشکاری مدرن، از جمله جوشکاری قوس الکتریکی (Arc Welding) معرفی شدند. نیکولای بناردوس (Nikolai Benardos) و استانیسلاو اولسوسکی (Stanisław Olszewski) در توسعه جوشکاری قوس الکتریکی نقش مهمی داشتند.
تکامل دستگاههای جوشکاری در قرن ۲۰
- دهه ۱۹۲۰: جوشکاری مقاومتی و گازی (Gas Welding) توسعه یافت. این تکنیکها برای اتصال قطعات کوچک و حساس کاربرد داشتند.
- دهه ۱۹۴۰: جوشکاری TIG و MIG گاز بیاثر تنگستن و گاز بیاثر فلزمعرفی شدند که برای صنایع پیشرفته مانند هوافضا و خودروسازی اهمیت پیدا کردند.
- دهه ۱۹۵۰: دستگاههای جوش اتوماتیک وارد بازار شدند و دقت و سرعت جوشکاری به طور قابل توجهی افزایش یافت.
دستگاههای جوشکاری مدرن
امروزه دستگاههای جوشکاری از تکنولوژیهای پیشرفتهای همچون کنترل دیجیتال، لیزر، و جوشکاری زیرآب بهره میبرند. این دستگاهها نه تنها در صنایع سنگین بلکه در پروژههای کوچک خانگی نیز کاربرد دارند.
تأثیر دستگاههای جوشکاری در صنعت
دستگاههای جوشکاری به عنوان یکی از ابزارهای کلیدی در صنایع ساختمانی، خودروسازی، کشتیسازی، و حتی پزشکی شناخته میشوند. این ابزارها باعث اتصال دقیقتر، استحکام بیشتر، و کاهش هزینههای تولید شدهاند.
آشنایی با انواع دستگاه جوش و کاربردهای آنها
امروزه جوشکاری یکی از مهمترین فرآیندها در صنایع مختلف است که از آن برای اتصال قطعات فلزی و غیر فلزی استفاده میشود. آشنایی با انواع دستگاه جوش و کاربردهای آنها برای انتخاب ابزار مناسب در هر پروژه از اهمیت بالایی برخوردار است. در این مقاله قصد داریم به بررسی انواع دستگاههای جوش و موارد استفاده از آنها بپردازیم.
انواع دستگاه جوش
جوشکاری قوس الکتریکی (Forge Welding)
جوشکاری با آهنگری (Forge Welding) یکی از قدیمیترین روشهای جوشکاری است که در آن دو قطعه فلزی به کمک گرما و فشار به هم متصل میشوند. این نوع جوشکاری به ویژه برای فلزات آهنی و فولادی استفاده میشود و معمولاً در صنایع دستی و آهنگریهای سنتی کاربرد دارد. در اینجا به مزایا و معایب این روش و نحوه عملکرد آن میپردازیم.
نحوه عملکرد جوشکاری با آهنگری
در این روش، قطعات فلزی ابتدا در کوره یا به کمک مشعل تا دمای بسیار بالایی (حدود 1000 تا 1200 درجه سانتیگراد) گرم میشوند تا به حدی نرم شوند که قابلیت تغییر شکل پیدا کنند. پس از آن، قطعات در حالت گرم تحت فشار قرار میگیرند، معمولاً به وسیله چکش یا پرس، تا با هم ترکیب شده و اتصال دائمی ایجاد شود. این فرایند بدون استفاده از جوش یا مواد افزودنی انجام میشود.
مزایای جوشکاری با آهنگری
- اتصال مقاوم و محکم: اتصال ایجاد شده در این روش معمولاً بسیار مقاوم و قوی است و به طور معمول از اتصالات جوشکاری معمولی بهتر است.
- استفاده از فلزات مختلف: این روش به خوبی برای اتصال انواع مختلف فلزات (مانند آهن، فولاد و …) به کار میرود.
- عدم نیاز به مواد پرکننده: بر خلاف برخی از روشهای جوشکاری دیگر که نیاز به سیم جوش یا مواد پرکننده دارند، در جوشکاری با آهنگری تنها گرما و فشار برای ایجاد اتصال کافی است.
- اتصال یکنواخت: این روش باعث میشود که هیچگونه تغییر شکل یا تخلخل در ناحیه جوش ایجاد نشود و اتصال کاملاً یکنواخت باشد.
معایب جوشکاری با آهنگری
- نیاز به تجهیزات خاص: این روش نیاز به تجهیزات ویژهای مانند کوره یا مشعلهای صنعتی و همچنین چکشهای سنگین دارد که ممکن است هزینههای اولیه بالایی را به همراه داشته باشد.
- زمانبر بودن: فرآیند جوشکاری با آهنگری زمانبر است، چرا که ابتدا باید قطعات را تا دمای مناسب گرم کرد و سپس تحت فشار قرار داد.
- محدودیت در مواد قابل استفاده: این روش بیشتر برای فلزات نرم و فولادی مناسب است و برای جوشکاری فلزات غیرآهنی یا آلیاژهای خاص مناسب نیست.
- نیاز به مهارت: انجام این روش نیاز به مهارت و تجربه بالایی دارد تا از آسیبدیدن قطعات یا ایجاد اتصالات ضعیف جلوگیری شود.
در نتیجه، جوشکاری با آهنگری یکی از روشهای سنتی و بسیار موثر برای اتصال فلزات است، اما به دلیل نیاز به تجهیزات خاص و مهارت بالا، در دنیای صنعتی مدرن کمتر مورد استفاده قرار میگیرد و بیشتر در صنایع دستی و آهنگریهای سنتی کاربرد دارد.
دستگاه جوشکاری قوس الکتریکی (Arc Welding) یکی از رایجترین روشهای جوشکاری است که در صنایع مختلف برای اتصال قطعات فلزی بهکار میرود. در این روش، از قوس الکتریکی بهعنوان منبع حرارت برای ذوب فلز پایه و فلز پرکننده استفاده میشود. در ادامه به بررسی مزایا، معایب و نحوه عملکرد این دستگاه میپردازیم:
مزایای دستگاه جوشکاری قوس الکتریکی
- هزینه پایین: دستگاههای جوشکاری قوس الکتریکی قیمت مناسبی دارند و به همین دلیل در مقایسه با سایر روشهای جوشکاری هزینه کمتری دارند.
- کاربرد گسترده: این دستگاهها در صنایع مختلف از جمله ساختمانسازی، تعمیرات خودرو، کشتیسازی و بسیاری دیگر کاربرد دارند.
- سهولت استفاده: جوشکاری قوس الکتریکی نسبت به بسیاری از روشهای دیگر سادهتر است و به مهارت خاصی نیاز ندارد.
- امکان جوشکاری در شرایط محیطی متفاوت: این روش در محیطهای باز و حتی در شرایط آب و هوایی نامساعد هم قابل انجام است.
- کیفیت بالا: جوشکاری قوس الکتریکی میتواند جوشهایی با کیفیت بالا و استحکام مناسب تولید کند.
معایب دستگاه جوشکاری قوس الکتریکی
- ایجاد دود و بخارات
- در این روش، گازهای سمی و دود زیادی تولید میشود که میتواند به سلامت جوشکار آسیب برساند.
- نیاز به دقت بالا
- در صورت عدم دقت کافی در تنظیم جریان الکتریکی و حرکت الکترود، کیفیت جوش پایین میآید.
- آسیب به الکترود
- الکترودها در طی فرآیند جوشکاری مصرف میشوند و نیاز به تعویض دارند که میتواند هزینههای اضافی ایجاد کند.
- ایجاد براده و خرابی در سطح جوش: اگر از شرایط مناسب برای انجام جوش استفاده نشود، سطح جوش ممکن است ناصاف و نامناسب باشد.
- نیاز به مهارت
- علیرغم سادگی نسبی، جوشکار باید تجربه و مهارت کافی در تنظیم دستگاه و استفاده از تکنیکهای صحیح داشته باشد.
نوع عملکرد دستگاه جوشکاری قوس الکتریکی
در جوشکاری قوس الکتریکی، الکترود که معمولاً از جنس فلز پرکننده است، به قطعه کار نزدیک میشود و قوس الکتریکی بین الکترود و قطعه کار برقرار میشود. این قوس الکتریکی حرارت زیادی تولید میکند که باعث ذوب فلزات میشود و پس از انجماد، اتصال محکمی بین قطعات فلزی ایجاد میشود. این روش معمولاً برای جوشکاری قطعات فلزی ضخیم و یا قطعاتی که نیاز به استحکام بالایی دارند، استفاده میشود.
در نهایت، جوشکاری قوس الکتریکی بهدلیل مزایای متعددی که دارد، یکی از محبوبترین روشهای جوشکاری در صنایع مختلف بهشمار میرود، اما معایبی مانند تولید دود و نیاز به مهارت بالا نیز در کنار آن وجود دارد.
جوشکاری مقاومتی و گازی (Gas Welding)
در فرآیند جوشکاری با گاز (Gas Welding)، از یک گاز قابل اشتعال (معمولاً اکسیژن و استیلن) برای تولید حرارت بالا استفاده میشود تا قطعات فلزی به هم جوش داده شوند. این نوع جوشکاری معمولاً برای جوش دادن فلزات نازک، تعمیرات و جوشکاری در محلهای دور از دسترس مناسب است.
مزایای جوشکاری با گاز
- پرتابل بودن: دستگاههای جوشکاری با گاز معمولاً قابل حمل هستند و میتوان از آنها در محیطهای مختلف و در جاهایی که دسترسی به برق وجود ندارد، استفاده کرد.
- هزینه پایین
- تجهیزات مورد نیاز برای جوشکاری با گاز نسبت به سایر روشهای جوشکاری مانند جوشکاری الکتریکی ارزانتر هستند.
- مناسب برای تعمیرات
- این نوع جوشکاری برای تعمیرات و جوش دادن قطعات نازک و ظریف مناسب است.
- امکان جوشکاری در فضاهای باز: به دلیل عدم نیاز به منابع برق، میتوان از این روش در محیطهای باز و خارج از کارگاه استفاده کرد.
معایب جوشکاری با گاز
- سرعت پایین: سرعت جوشکاری با گاز نسبت به سایر روشها مانند جوشکاری الکتریکی پایینتر است.
- کیفیت پایینتر جوش
- در مقایسه با جوشکاری قوس الکتریکی یا سایر روشها، جوشهای ایجاد شده ممکن است استحکام کمتری داشته باشند.
- نیاز به گاز
- جوشکاری با گاز نیاز به تهیه گازهایی مانند استیلن و اکسیژن دارد که ممکن است هزینهبر و نیازمند دقت در ذخیرهسازی باشد.
- خطرات ایمنی
- در این نوع جوشکاری به دلیل استفاده از گازهای قابل اشتعال، خطر آتشسوزی یا انفجار وجود دارد.
نوع عملیات جوشکاری با گاز
در جوشکاری با گاز، دو گاز اصلی (اکسیژن و استیلن) از طریق لولهها و شلنگها به مشعل میرسند. در مشعل، این گازها با هم ترکیب شده و شعلهای با دمای بسیار بالا (حدود ۳۲۰۰ درجه سانتیگراد) ایجاد میکنند که میتواند فلزات را ذوب کرده و آنها را به هم جوش دهد. جوشکاری با گاز به دو نوع اصلی تقسیم میشود:
جوشکاری با شعله
در این روش، شعله به صورت مستقیم روی لبههای قطعات قرار داده میشود تا آنها ذوب شده و به هم جوش بخورند.
جوشکاری با قوس گازی
این روش ترکیبی از جوشکاری با گاز و قوس الکتریکی است که برای جوش دادن قطعات ضخیمتر استفاده میشود.
این روش برای پروژههایی که نیاز به دقت و سرعت بالا ندارند، اما در عوض نیاز به حمل و نقل آسان و هزینه کمتر دارند، بسیار مناسب است.
دستگاه جوش الکترود دستی (MMA)
دستگاه جوش الکترود دستی (MMA) یکی از رایجترین انواع دستگاههای جوشکاری است که برای جوش دادن قطعات فلزی با استفاده از الکترود مصرفی مورد استفاده قرار میگیرد. در این روش، الکترود جوش به صورت مستقیم به قطعات فلزی متصل شده و جریان الکتریکی باعث ذوب شدن آن و ایجاد اتصال بین قطعات میشود.
مزایا
- قابلیت استفاده در شرایط مختلف: این دستگاهها برای جوشکاری در فضای باز و شرایط سخت محیطی مناسب هستند و به دلیل طراحی خاص، حتی در محیطهای با جریان هوای زیاد نیز میتوان از آنها استفاده کرد.
- قیمت مقرون به صرفه
- دستگاه جوش MMA به نسبت دستگاههای جوش دیگر هزینه کمتری دارد و برای جوشکارانی که نیاز به دستگاهی با هزینه پایین دارند، گزینه مناسبی است.
- سادگی و راحتی در استفاده
- این دستگاهها به سادگی قابل حمل و استفاده هستند و نیاز به آموزش پیچیدهای ندارند. همچنین، تعمیرات و نگهداری آنها نسبت به دیگر دستگاهها سادهتر است.
- جوشکاری انواع فلزات
- با استفاده از این دستگاه میتوان انواع فلزات مانند فولاد، چدن، استیل و آلیاژهای مختلف را جوش داد.
کاربردها
- تعمیرات صنعتی
- جوشکاری در ساختمانسازی
- استفاده در کارگاههای کوچک و متوسط
معایب
- کیفیت جوش متغیر
- کیفیت جوش به شدت به مهارت جوشکار و انتخاب صحیح الکترود بستگی دارد. در نتیجه، جوشکاری با این دستگاه به دقت و تجربه بیشتری نیاز دارد.
- ایجاد دود زیاد
- در حین جوشکاری، دستگاههای MMA دود زیادی تولید میکنند که ممکن است برای جوشکار و دیگر افراد در محیطهای بسته خطرناک باشد.
- نیاز به کنترل جریان
- جوشکار باید به دقت جریان برق را تنظیم کند، زیرا تغییرات در جریان میتواند باعث خرابی جوش یا کیفیت پایین آن شود.
- الکترودهای مصرفی
- از آنجایی که الکترود در این دستگاهها مصرف میشود، نیاز به تهیه مداوم الکترودهای جدید وجود دارد.
نوع عملکرد
در دستگاه جوش MMA، جریان الکتریکی از طریق کابل به الکترود منتقل میشود. الکترود جوش در تماس با سطح فلز قرار میگیرد و باعث ذوب شدن فلز و الکترود میشود. این ذوب شدن باعث اتصال فلزات به یکدیگر میشود. پس از ذوب شدن الکترود، یک قوس الکتریکی بین الکترود و سطح فلز ایجاد میشود که این قوس حرارت زیادی تولید میکند و باعث ذوب و اتصال فلزات میشود.
این دستگاه به دلیل قابلیت تنظیم جریان الکتریکی، جوشکاری انواع مختلف فلزات و ضخامتهای متفاوت را ممکن میسازد، اما نیاز به تجربه و مهارت جوشکار دارد تا بهترین نتیجه حاصل شود.
دستگاه جوش MIG/MAG
دستگاه جوش MIG/MAG یکی از انواع دستگاههای جوشکاری است که در صنایع مختلف برای جوش دادن فلزات استفاده میشود. این دستگاه به دو نوع اصلی MIG (Metal Inert Gas) و MAG (Metal Active Gas) تقسیم میشود که تفاوت اصلی آنها در نوع گاز محافظ است.
مزایای دستگاه جوش MIG/MAG
- سرعت بالا
- جوشکاری با دستگاه MIG/MAG به دلیل استفاده از الکترود پیوسته، سرعت بالایی دارد و برای جوشهای طولانی و حجیم مناسب است.
- کیفیت بالا
- این روش جوشکاری به دلیل کنترل دقیق روی پارامترهای جوش، جوشهای تمیز و با کیفیت بالا تولید میکند.
- سهولت در استفاده: دستگاه جوش MIG/MAG کاربری آسانی دارد و نیاز به مهارت خاصی ندارد. این امر باعث میشود برای اپراتورهای کم تجربه نیز قابل استفاده باشد.
- جوشهای زیبا
- این روش به دلیل جریان یکنواخت و ثابت، جوشهای زیبا و بدون عیوب زیادی تولید میکند.
- مناسب برای انواع فلزات: دستگاه MIG/MAG برای جوشکاری انواع فلزات از جمله فولاد، آلومینیوم و استیل مناسب است.
- مناسب برای مواد فلزی نازک
کاربردها
- صنایع خودروسازی
- ساخت مخازن و لولهها
- صنایع تولیدی بزرگ
معایب دستگاه جوش MIG/MAG
هزینه بالای تجهیزات
دستگاه جوش MIG/MAG به دلیل پیچیدگی و تجهیزات خاص خود، هزینه بالاتری نسبت به روشهای جوشکاری دیگر مانند جوشکاری با الکترود دارد.
- نیاز به گاز محافظ
- در جوشکاری MIG، نیاز به گاز محافظ خنثی (مثل آرگون) و در جوشکاری MAG نیاز به گازهای فعال (مثل CO2 یا مخلوطی از آرگون و CO2) است. این امر ممکن است هزینههای عملیاتی را افزایش دهد.
- محدودیت در جوشکاری در فضاهای باز: به دلیل استفاده از گاز محافظ، دستگاههای MIG/MAG برای جوشکاری در فضای باز و در شرایط باد زیاد مناسب نیستند.
- جوشکاری محدود به ضخامتهای خاص
- این روش جوشکاری برای جوشکاری فلزات با ضخامتهای بسیار زیاد یا خیلی نازک ممکن است محدودیتهایی داشته باشد.
نوع عملکرد دستگاه جوش MIG/MAG
در جوشکاری MIG، یک الکترود فلزی که به صورت سیم پیوسته است از طریق تفنگ جوشکاری به ناحیه جوش هدایت میشود. گاز محافظ به این الکترود و ناحیه جوش منتقل میشود تا از اکسید شدن فلز جلوگیری کند و جوش با کیفیت بالایی به دست آید. در جوشکاری MAG، از گازهای فعال به جای گازهای خنثی استفاده میشود که این گازها به واکنشهای شیمیایی کمک میکنند و باعث بهبود کیفیت جوش میشوند.
در کل، دستگاه جوش MIG/MAG یکی از محبوبترین و کارآمدترین روشهای جوشکاری برای صنایع مختلف است که به دلیل سرعت و کیفیت بالا، در بسیاری از کارخانهها و کارگاهها کاربرد دارد.
دستگاه جوش TIG
دستگاه جوش TIG (Tungsten Inert Gas) یکی از انواع دستگاههای جوشکاری است که برای جوش دادن فلزات به کار میرود. این دستگاه از الکترود تنگستن غیر مصرفی استفاده میکند و برای جوشکاری با دقت و کیفیت بالا طراحی شده است. در اینجا به مزایا، معایب و نوع عملکرد این دستگاه پرداخته میشود:
مزایای دستگاه جوش
- کیفیت جوش بالا
- جوشهای تولید شده توسط دستگاه TIG بسیار تمیز و دقیق هستند و نیاز به پسپردازش کمتری دارند.
- امکان جوشکاری مواد مختلف
- دستگاه TIG برای جوشکاری انواع فلزات از جمله فولاد ضد زنگ، آلومینیوم، مس، تیتانیوم و … مناسب است.
- عدم ایجاد پاشش: در جوشکاری TIG، چون از الکترود تنگستن غیر مصرفی استفاده میشود، پاشش فلز مذاب کاهش مییابد و سطح جوش تمیزتر باقی میماند.
- امکان جوشکاری در موقعیتهای مختلف: این دستگاه برای جوشکاری در موقعیتهای دشوار و محدود مناسب است و میتوان به راحتی در زوایای مختلف جوشکاری انجام داد.
- دقت بالا: کنترل دقیق جریان و ولتاژ در دستگاه TIG باعث میشود که جوشکاری با دقت بالا و به طور دقیق انجام شود.
- مناسب برای مواد نازک و حساس
- ایجاد جوش با استحکام بالا
کاربردها
- صنایع هوایی
- جوشکاری لولههای فشار قوی
- تولید قطعات پزشکی
معایب دستگاه جوش TIG
- سرعت پایین
- نسبت به برخی روشهای دیگر جوشکاری (مانند جوشکاری MIG یا قوس الکتریکی)، سرعت جوشکاری در دستگاه TIG پایینتر است.
- نیاز به مهارت بالا
- جوشکاری با دستگاه TIG نیازمند تجربه و دقت زیادی است و به راحتی نمیتوان آن را به افراد مبتدی توصیه کرد.
- هزینه بالا
- دستگاههای جوش TIG معمولاً گرانتر از دستگاههای جوشکاری دیگر هستند و نیاز به تجهیزات جانبی بیشتری دارند.
- نیاز به گاز محافظ
- این دستگاه برای عملکرد بهتر نیاز به گاز محافظ (مثل آرگون یا هلیوم) دارد که هزینهبردار است و باید بهطور مرتب تامین شود.
نوع عملکرد دستگاه جوش TIG
در جوشکاری TIG، الکترود تنگستن که غیر مصرفی است، به طور مستقیم با قطعه کار در تماس نیست. دستگاه با استفاده از جریان الکتریکی، قوس الکتریکی بین الکترود و قطعه کار ایجاد میکند. این قوس بهطور مداوم حرارت لازم را برای ذوب فلز و اتصال دو قطعه تامین میکند. در این فرآیند، گاز محافظ (معمولاً آرگون) بهطور مداوم در اطراف ناحیه جوش جریان دارد تا از آلودگی هوا و اکسید شدن فلز جوش جلوگیری کند. سیم جوش در این دستگاه بهطور جداگانه به ناحیه جوش وارد میشود و به ذوب شدن قطعههای فلزی کمک میکند.
در مجموع، دستگاه جوش TIG برای جوشکاری دقیق و با کیفیت بالا بسیار مناسب است، اما برای کاربرانی که به سرعت و راحتی بیشتر نیاز دارند، ممکن است گزینه مناسبی نباشد.
دستگاه جوش زیرپودری (SAW)
دستگاه جوش زیرپودری (Submerged Arc Welding – SAW) یکی از فرآیندهای پیشرفته جوشکاری است که در صنایع سنگین و پروژههای بزرگ مورد استفاده قرار میگیرد. در ادامه به توضیح مزایا، معایب و نحوه عملکرد این دستگاه پرداختهایم
مزایای دستگاه جوش زیرپودری (SAW)
- کیفیت بالای جوش
- این روش به دلیل حفاظت کامل از قوس در برابر هوا، جوشی با کیفیت بالا و بدون ترک یا تخلخل ایجاد میکند.
- سرعت جوشکاری بالا
- به دلیل استفاده از قوس الکتریکی قوی و تغذیه مداوم الکترود، سرعت جوشکاری نسبت به روشهای دیگر بیشتر است.
- عدم تولید اشعه مضر: به دلیل پنهان بودن قوس، اپراتور در معرض تابش اشعه ماوراء بنفش یا نور خیرهکننده قرار نمیگیرد.
- مناسب برای قطعات ضخیم: این دستگاه برای جوشکاری قطعات ضخیم و بزرگ بسیار مناسب است.
- کاهش مصرف گاز محافظ: برخلاف روشهای دیگر مانند MIG یا TIG، نیاز به گاز محافظ جداگانه ندارد
کاربردها
- صنایع نفت و گاز
- ساخت مخازن تحت فشار
- تولید سازههای فلزی بزرگ
- کشتیسازی
- راهآهن و پلسازی
معایب دستگاه جوش زیرپودری (SAW)
- محدودیت در موقعیتهای جوشکاری: این دستگاه عمدتاً برای جوشکاری در حالتهای افقی یا تخت طراحی شده و در موقعیتهای عمودی یا سقفی کارایی ندارد.
- هزینه اولیه بالا
- خرید دستگاه، پودر محافظ و تجهیزات جانبی میتواند هزینهبر باشد.
- نیاز به تجهیزات حجیم: این دستگاه فضای زیادی اشغال میکند و برای محیطهای کاری کوچک مناسب نیست.
- عدم قابلیت استفاده برای جوشکاری نازک: برای ورقهای با ضخامت کم مناسب نیست و ممکن است باعث ذوب بیش از حد یا تغییر شکل قطعه شود.
- نیاز به حذف سرباره: پس از هر عملیات، سرباره و پودر باقیمانده باید تمیز شوند که زمانبر است.
نحوه عملکرد دستگاه جوش زیرپودری (SAW)
- پودر محافظ
- این فرآیند از پودر جوشکاری خاصی به عنوان محافظ استفاده میکند. این پودر روی قوس الکتریکی بین الکترود و قطعه کار پخش شده و قوس را به طور کامل میپوشاند.
- قوس الکتریکی مخفی
- قوس الکتریکی در زیر لایهای از پودر محافظ ایجاد میشود و همین باعث کاهش تابش نور و جرقه میشود.
- الکترود مصرفی
- الکترود به صورت مداوم تغذیه میشود و به عنوان منبع فلز جوش عمل میکند.
- ذوب پودر
- بخشی از پودر محافظ در اثر حرارت ذوب شده و به شکل سرباره محافظ روی جوش باقی میماند.
- خروج سرباره و پودر باقیمانده: پس از سرد شدن جوش، سرباره و پودر اضافی از روی جوش برداشته میشود.
این روش به دلیل راندمان بالا و کیفیت جوش بینظیر، یکی از روشهای محبوب در جوشکاری صنعتی است، اما به دلیل محدودیتها و هزینههای اولیه نیاز به بررسی دقیق پیش از استفاده دارد.
دستگاه جوش نقطهای (Spot Welding Machine)
نوع عملکرد دستگاه جوش نقطهای
دستگاه جوش نقطهای یکی از روشهای متداول در جوشکاری است که برای اتصال دو قطعه فلزی بهطور مستقیم و بدون نیاز به الکترود یا مواد پرکننده استفاده میشود.
عملکرد اصلی
در این دستگاه، دو الکترود فلزی به قطعاتی که باید جوش داده شوند، فشار وارد کرده و جریان الکتریکی قوی از طریق این نقاط عبور میکند.
مراحل
قطعات فلزی بین الکترودها قرار میگیرند.
جریان الکتریکی به سرعت گرم شده و نقطهای از فلز را ذوب میکند
مزایای دستگاه جوش نقطهای
- سرعت بالا
- این روش بسیار سریع است و برای تولید انبوه و اتصالات متعدد در صنایع خودروسازی، ساخت لوازم خانگی، و تجهیزات فلزی ایدهآل است.
- کیفیت اتصال
- جوشکاری نقطهای، اتصال قوی و قابل اعتمادی ایجاد میکند که برای مواد نازک مانند ورقهای فلزی بسیار مناسب است.
- کاهش هزینهها
- به دلیل عدم نیاز به مواد پرکننده یا گازهای محافظ، هزینههای مصرفی پایین است.
- سادگی و خودکارسازی
- این روش بهراحتی قابل خودکارسازی است و در خطوط تولید کارخانهها به کار میرود.
- کاهش تغییرات حرارتی
- به دلیل تمرکز گرما در یک نقطه کوچک، اعوجاج یا تغییر شکل حرارتی در اطراف نقطه جوش به حداقل میرسد.
معایب دستگاه جوش نقطهای
- محدودیت در ضخامت فلزات
- این دستگاه برای فلزات با ضخامت زیاد مناسب نیست، زیرا جوشکاری در نقاط ضخیمتر مشکل است.
- نیاز به تجهیزات پیشرفته
- دستگاههای جوش نقطهای پیشرفته ممکن است گرانقیمت باشند و نیاز به مهارت برای تنظیم دقیق فشار و جریان دارند.
- عدم انعطافپذیری
- این روش فقط برای جوشکاری نقاط خاص مناسب است و برای ایجاد جوشهای طولانی یا پیچیده کاربرد ندارد.
- کیفیت اتصال محدود
- اگر تنظیمات دستگاه به درستی انجام نشود، ممکن است جوش ضعیفی ایجاد شود که استحکام مورد نظر را نداشته باشد.
کاربردها
- صنایع خودروسازی :اتصال قطعات بدنه خودرو.
- تولید لوازم خانگی :مانند ماشین لباسشویی و یخچال.
- تجهیزات فلزی سبک :ساخت کابینتها و قفسههای فلزی.
در کل، دستگاه جوش نقطهای برای پروژههایی که نیاز به اتصال سریع و اقتصادی قطعات فلزی دارند، بسیار مناسب است، اما برای کاربردهای سنگین یا پیچیده ممکن است به روشهای دیگری نیاز باشد.
دستگاه جوش پلاسما
. دستگاه جوش پلاسما یکی از تجهیزات پیشرفته در صنعت جوشکاری است که با استفاده از گاز یونیزهشده (پلاسما) قادر به ایجاد دمای بسیار بالا برای برش یا جوش مواد مختلف میباشد. در ادامه، توضیحاتی در مورد نحوه عملکرد، مزایا و معایب این دستگاه ارائه میشود:
مزایای دستگاه جوش پلاسما
- دقت بالا
- این دستگاه قابلیت جوشکاری بسیار دقیق و کنترلشده را برای مواد نازک و حساس دارد.
- دمای بالا
- پلاسما دمای بسیار بالایی ایجاد میکند که جوشکاری و برش مواد سخت مانند فولاد ضدزنگ، آلومینیوم و تیتانیوم را امکانپذیر میسازد.
- سرعت کار
- سرعت عملکرد این دستگاه نسبت به روشهای سنتی جوشکاری بالاتر است.
- کیفیت جوش
- جوشهای ایجادشده توسط این دستگاه از کیفیت بالایی برخوردارند و بهندرت نیاز به پرداخت اضافی دارند.
- کاربرد گسترده
- دستگاه جوش پلاسما برای برش و جوشکاری انواع مواد فلزی و غیر فلزی مناسب است.
معایب دستگاه جوش پلاسما
- هزینه بالا
- خرید و نگهداری این دستگاه نسبت به دستگاههای جوش معمولی گرانتر است.
- نیاز به تخصص
- استفاده از دستگاه جوش پلاسما نیاز به آموزش و مهارت بالا دارد.
- مصرف انرژی
- دستگاههای جوش پلاسما انرژی بیشتری نسبت به دستگاههای جوش معمولی مصرف میکنند.
- استفاده محدود در شرایط خاص
- برای مواد ضخیمتر ممکن است نیاز به دستگاههای بزرگتر و قدرتمندتر باشد.
کاربردها
- جوشکاری در صنایع هوافضا، خودروسازی، کشتیسازی، و تولید تجهیزات پزشکی.
- برش دقیق و سریع مواد فلزی در پروژههای صنعتی.
- جوشکاری مواد حساس مانند آلومینیوم و تیتانیوم که نیاز به دقت و کیفیت بالایی دارند.
- در کل، دستگاه جوش پلاسما یک انتخاب مناسب برای کارهایی است که به دقت و کیفیت بالا نیاز دارند، اما هزینهها و نیاز به مهارت تخصصی را نیز باید در نظر گرفت.
نحوه عملکرد دستگاه جوش پلاسما
- ایجاد پلاسما
- پلاسما حالتی از ماده است که در آن گاز به شدت گرم شده و الکترونها از اتمها جدا میشوند. دستگاه جوش پلاسما با ایجاد قوس الکتریکی در داخل گاز (معمولاً آرگون یا نیتروژن)، پلاسما تولید میکند.
- انتقال حرارت
- پلاسما به عنوان یک رسانای بسیار قوی عمل کرده و گرمای زیادی تولید میکند که برای ذوب و اتصال قطعات استفاده میشود.
- کنترل دقیق
- دستگاه به کاربر این امکان را میدهد که دما، شدت جریان و نوع گاز را بهطور دقیق کنترل کند، بنابراین برای کارهای حساس و ظریف مناسب است.
نکات مهم در انتخاب دستگاه جوش
نوع ماده
نوع موادی که قصد جوشکاری آنها را دارید، یکی از عوامل اصلی در انتخاب دستگاه مناسب است. برای مثال، دستگاه TIG برای مواد نازک و حساس مناسبتر است.
نوع پروژه
پروژههای بزرگ صنعتی معمولاً به دستگاههایی با قدرت بالا مانند SAW نیاز دارند، در حالی که پروژههای خانگی ممکن است با دستگاه MMA به خوبی انجام شوند.
بودجه
هزینه خرید و نگهداری دستگاهها نیز باید مورد توجه قرار گیرد. دستگاههای MIG/MAG و TIG معمولاً هزینه بالاتری نسبت به MMA دارند.
در نهایت، اگر در انتخاب دستگاه مناسب نیاز به مشاوره دارید میتوانید با کارشناسان ابزارباز تماس بگیرید.